INTERVIEW WITH TINA LUNDELL AT ELIS
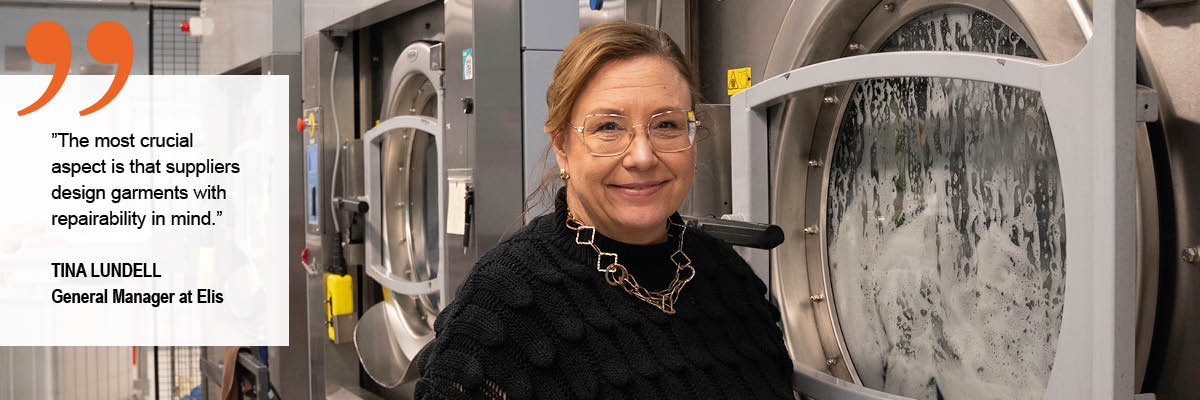
As a leader within the textile and hygiene service sector with a focus on a circular business model for over 70 years, Elis specialises in renting out, collecting, washing and repairing items across the entire lifecycle, until the product can’t be repaired again to perform its original purpose.
Elis is much more than just a laundromat. They offer sustainable, time-saving and customised services including rental, laundry, maintenance and delivery of quality textiles, with quality and lifespan combining to ensure sustainability. That’s why they’ve been a natural and important partner to us at Tranemo for so many years.
We had the opportunity to interview Tina Lundell, General Manager at Elis in Angered, Gothenburg, to discuss sustainability and quality assurance with us and how our collaborations affect our products and their services.
Elis works hard to ease the headaches that come with workwear. When renting out PPE to customers, Elis ensures the clothes have the right fit, and can quickly swap out or remove clothes when employees leave or start – avoiding unnecessary purchases and stockpiles of old clothes.
Elis picks up and delivers the workwear, and when the textiles come to their facility, they are sorted by material and the type of grime they’ve been in contact with before washing. 80% of a garment's environmental impact occurs in the manufacturing phase. The more times it can be used, the lesser the impact on the environment. The way the items are washed is essential here:
“First of all, we wash it the right way,” says Tina. “We wash it with the right washing programmes that are adapted to the type of dirt the garment contains, so that it’s washed in the most efficient way.”
“we wash it the right way, with the programmes that are adapted to the type of dirt the garment contains.”
The only things Elis adds during the washing process are water and detergents. However, their customers work in many different industries, and it’s common for clothes to be contaminated with substances like heavy metals – which end up in the waste water after the cleaning process. To prevent these substances damaging the environment, Elis has built its own water treatment plant to make sure hazardous materials aren’t released into the environment.
“There are things that should not go down the drain,” explains Tina. “That’s why we have emission rights and take monthly water samples, which we send for analysis and keep track of what we’re allowed to discharge. It’s very important.”
The textiles are also manually checked to see if there are any holes or tears in the PPE. If they happen to find a tear, the item will be mended with the correct materials to maintain the certifications of the PPE and ensure they still offer the same type and correct amount of protection as previously.
We had the opportunity to interview Tina Lundell at Elis Angered, Gothenburg, discussing the significance of extending the lifespan of our customers' garments and how we can assist in ensuring their PPE is of the highest quality.
“We repair the clothes until they are no longer reasonable to repair. And they are always repaired with materials that correspond to the requirements of the garment. The flameretardant garments are repaired with flameretardant material, and so on.”
Circularity is important, explains Tina: “That's probably the main thing, that we make sure that it's repaired, that it doesn't become a waste product. It is repaired until it can no longer be repaired. And then it becomes something else when it's discarded, so it doesn't go to incineration either, but becomes something else. It gets a new life in some form.”
By doing this Elis makes sure their customers’ employees are safe while wearing PPE rented from them. In doing this, they also put pressure on their own suppliers to deliver garments and products of a higher quality.
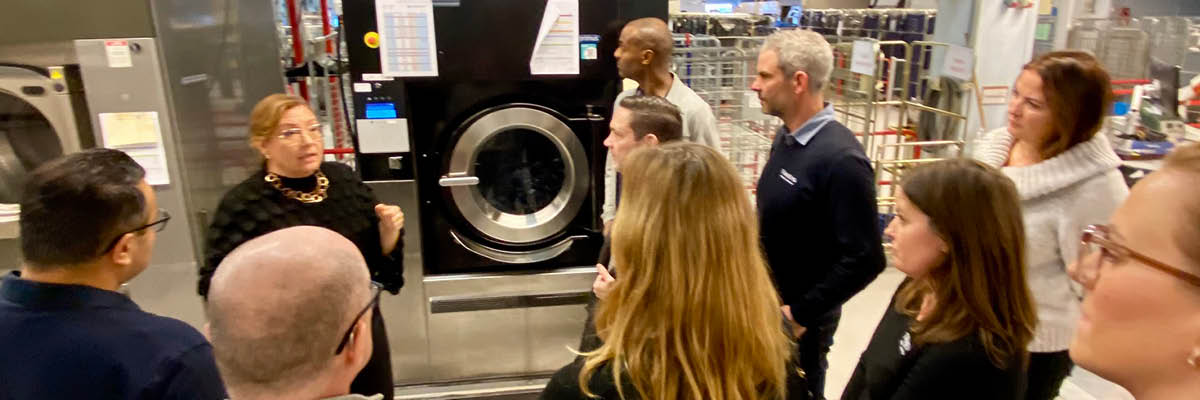
“The most important thing is that the suppliers think about the actual repair of the garment.”
“The most important thing is that the suppliers, when designing the garment, think about the actual repair of the garment, that it is possible to repair it. Because this is essential for us as we extend the lifespan of the garments, mostly with mending and proper handling. When I worked in the automotive industry, they said "design for after market", and it's really just the same thing here. It’s also important for suppliers to choose materials that last in their garments. It’s important that you invest in good reflectors, that you invest in good buttons, that you invest in zips that last and that you invest in fabric that actually lasts.”
Tina continues: “The quality of a garment has a direct effect on its lifespan, and the difference is visibly noticeable. Low-quality garments they lose colour quickly, their shape, their reflectors and so on.”
“Those are things I think about for my part. It’s also important for the customer, especially if their employees’ appearance is an important part of their brand.”
That’s something we take very seriously at Tranemo as well. It’s important that employees’ garments represent the company they work for. And when we make garment recommendations, it’s essential that the garments feel good to wear and use over time. That’s why we offer repairs in all the countries we operate in, and why Elis maintains reserve stocks of essential garments. This ensures that even if a garment has a hole or an employee quits, you won’t be left with garments that can’t be used. "If you are a rental customer with us, we do not throw away the garments, they live on until they are absolutely finished," explains Tina.
“We do not throw away the garments, they live on until they are absolutely finished.”
Elis’ approach to repairs is completely different to the disposable culture that consumers might be used to. “If a zip breaks on a garment and no-one repairs it, it’s easy to just throw it away. Even if it’s a two-week old jacket, and you’ve got it stuck somewhere or torn it, you can end up throwing away 2500 SEK if you don’t repair it. So repairing is very important, especially a well-done repair. We are not tailors, but we repair so that customers can see the clothes retain their functionality,” Tina says.
Here we have had a close collaboration, both in making sure Elis has been equipped with the right knowledge to repair Flame Retardant PPE, as well as with the materials and guidelines they need to retain the certifications of the garments. But our cooperation goes both ways - Elis testwashes all our textiles and new products prior to launch, to make sure they are approved for industrial washing before they even arrive at our customers’ doors. This is just one way our partnership boosts the quality and performance of our garments and ensures reliable and sustainable workwear for the most demanding operations.